大輸液生產線典型流程 洗瓶烘干滅菌灌裝加塞軋蓋滅菌燈檢貼標包裝
大輸液(如生理鹽水等)的生產是一個高度自動化、無菌要求嚴格的過程。以下是對各環節的詳細解析,涵蓋操作要點、設備類型及質量控制措施:
1. 洗瓶
目的:去除玻璃瓶(或塑料瓶)內外的微粒、灰塵、微生物等污染物。
設備:超聲波清洗機、高壓噴淋系統。
操作要點:
超聲波利用空化效應分解頑固污漬,噴淋水為注射用水(WFI)。
清洗后需用壓縮空氣吹干殘留水漬。
質量控制:目檢或攝像頭抽查瓶內清潔度,電導率檢測沖洗水純度。

2. 烘干滅菌
目的:干燥并滅菌空瓶,避免二次污染。
設備:隧道式烘箱(層流熱風滅菌),常見溫度300℃以上,時間≥5分鐘。
滅菌驗證:需進行熱分布試驗,確保各點溫度達標,生物指示劑(如嗜熱脂肪芽孢桿菌)驗證滅菌效果。
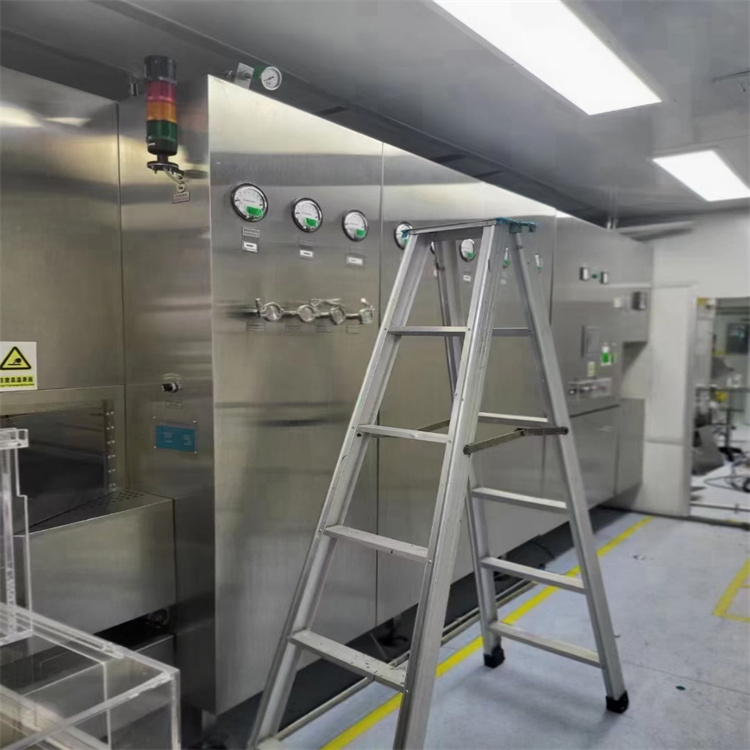
3. 灌裝
目的:精確注入藥液,嚴格無菌操作。
設備:全自動灌裝機(蠕動泵/伺服泵),灌裝區為潔凈環境(ISO 4.8)。
控制要點:
裝量精度:定期用稱重法或流量計校準,誤差≤±1%。
防污染:灌裝頭配備層流罩,藥液經0.22μm濾器除菌過濾。

4. 加塞
目的:用無菌膠塞初步密封瓶口。
設備:真空加塞機或機械壓塞機。
關鍵參數:膠塞預清洗滅菌(硅化處理),壓塞深度需一致,避免過緊(瓶口破裂)或過松(泄漏)。
5. 軋蓋
目的:鋁蓋壓緊固定膠塞,確保運輸中密封性。
設備:旋轉式軋蓋機,壓力可調。
檢測:在線視覺檢測鋁蓋平整度,抽樣進行啟封力測試(通常≥15N)。
6. 滅菌(終端滅菌)
目的:殺滅灌裝后可能引入的微生物,確保產品無菌。
方法:高壓蒸汽滅菌(如121℃, 15分鐘),或水浴滅菌(適用于熱敏感產品)。
驗證:需進行熱穿透試驗,Fo值(滅菌致死值)≥8分鐘,生物指示劑驗證。

7. 燈檢
目的:剔除含異物、微粒或密封缺陷的產品。
方式:
人工燈檢:在暗室中用背光目視檢查,檢出率約70%-80%。
自動燈檢機:高速攝像頭結合AI算法,檢測精度達99%以上,可識別≥50μm微粒。
抽樣標準:按《中國藥典》可見異物檢查法(如抽檢20瓶,不合格率≤1瓶)。
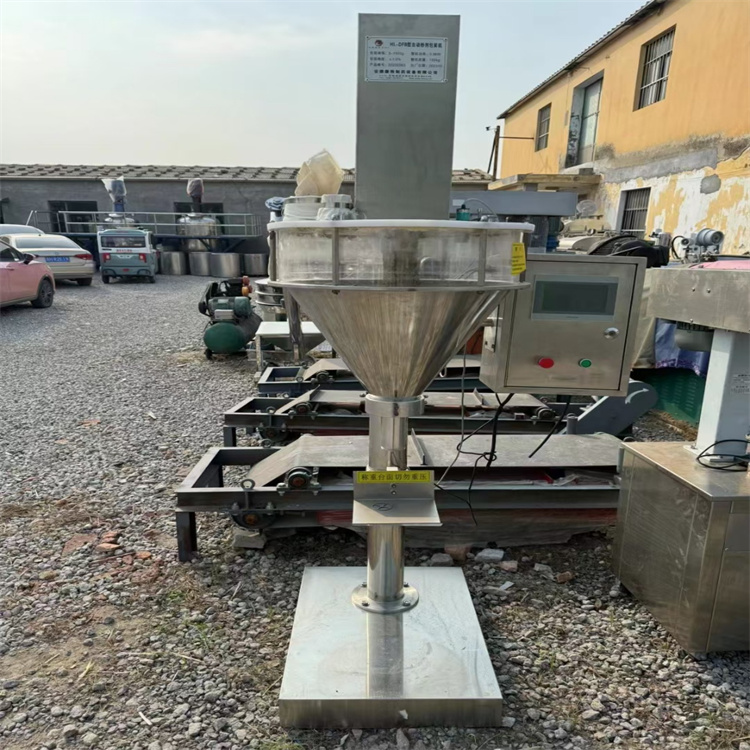
8. 貼標
目的:標注產品信息(品名、批號、有效期等),符合法規要求。
設備:自動貼標機(光學定位防貼歪)。
核對內容:電子監管碼、批號打印清晰度,標簽材質需耐滅菌高溫。

9. 包裝
目的:防塵防潮,便于運輸和儲存。
流程:自動裝盒(說明書、輸液管配套)、裹膜、裝箱。
追溯系統:每箱賦二維碼,記錄生產批次、滅菌參數等數據。
關鍵質量控制點(QC)
環境監測:灌裝區懸浮粒子、沉降菌定期檢測(符合GMP附錄1)。
無菌保證:培養基灌裝試驗(每年2次,模擬生產,污染率<0.1%)。
穩定性考察:留樣產品加速試驗(40℃/RH75%,6個月)評估有效期。
特別說明:兩次滅菌的意義
空瓶滅菌:確保容器無菌,避免灌裝前的二次污染。
終端滅菌:作為最終保障,即使灌裝中有微生物侵入,仍可殺滅。
通過上述流程的嚴格管控,大輸液產品可達到無菌、無熱原、無可見異物的質量要求,確保患者用藥安全。